A carton manufacturer produces two sizes of carton for a fortune 100 logistics company. The logistics company has agreed to buy the cartons for next 12 months. The carton manufacturer now has tasked their operations manager to identify the number of cartons to produce for each size to achieve maximum revenue. When sold to the logistics company, carton A5 sells for 6 dollars a piece and carton C5 sells for 8 dollars a piece. The carton manufacturer has a labor hours capacity of 8,300 hours and budget for raw material limited to $ 185,580. Carton A5 utilizes 0.09 hours of labor and $2 of material cost per piece whereas, carton C5 utilizes 0.12 hours of labor and $2.75 of material cost per piece. Formulate a LP model and solve in excel solver to calculate the optimal quantities of each type leading to maximizing the revenue and satisfying all constraints.
A carton manufacturer produces two sizes of carton for a fortune 100 logistics company. The logistics company has agreed to buy the cartons for next 12 months. The carton manufacturer now has tasked their operations manager to identify the number of cartons to produce for each size to achieve maximum revenue. When sold to the logistics company, carton A5 sells for 6 dollars a piece and carton C5 sells for 8 dollars a piece. The carton manufacturer has a labor hours capacity of 8,300 hours and budget for raw material limited to $ 185,580. Carton A5 utilizes 0.09 hours of labor and $2 of material cost per piece whereas, carton C5 utilizes 0.12 hours of labor and $2.75 of material cost per piece. Formulate a LP model and solve in excel solver to calculate the optimal quantities of each type leading to maximizing the revenue and satisfying all constraints.
Cornerstones of Cost Management (Cornerstones Series)
4th Edition
ISBN:9781305970663
Author:Don R. Hansen, Maryanne M. Mowen
Publisher:Don R. Hansen, Maryanne M. Mowen
Chapter20: Inventory Management: Economic Order Quantity, Jit, And The Theory Of Constraints
Section: Chapter Questions
Problem 7E: Ottis, Inc., uses 640,000 plastic housing units each year in its production of paper shredders. The...
Related questions
Question

Transcribed Image Text:A carton manufacturer produces two sizes of carton for a fortune 100 logistics company. The logistics
company has agreed to buy the cartons for next 12 months. The carton manufacturer now has tasked their
operations manager to identify the number of cartons to produce for each size to achieve maximum
revenue. When sold to the logistics company, carton A5 sells for 6 dollars a piece and carton C5 sells for 8
dollars a piece.
The carton manufacturer has a labor hours capacity of 8,300 hours and budget for raw material limited to $
185,580.
Carton A5 utilizes 0.09 hours of labor and $2 of material cost per piece whereas, carton C5 utilizes 0.12
hours of labor and $2.75 of material cost per piece.
Formulate a LP model and solve in excel solver to calculate the optimal quantities of each type leading to
maximizing the revenue and satisfying all constraints.
Expert Solution

This question has been solved!
Explore an expertly crafted, step-by-step solution for a thorough understanding of key concepts.
Step by step
Solved in 2 steps

Recommended textbooks for you
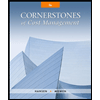
Cornerstones of Cost Management (Cornerstones Ser…
Accounting
ISBN:
9781305970663
Author:
Don R. Hansen, Maryanne M. Mowen
Publisher:
Cengage Learning
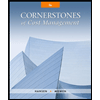
Cornerstones of Cost Management (Cornerstones Ser…
Accounting
ISBN:
9781305970663
Author:
Don R. Hansen, Maryanne M. Mowen
Publisher:
Cengage Learning